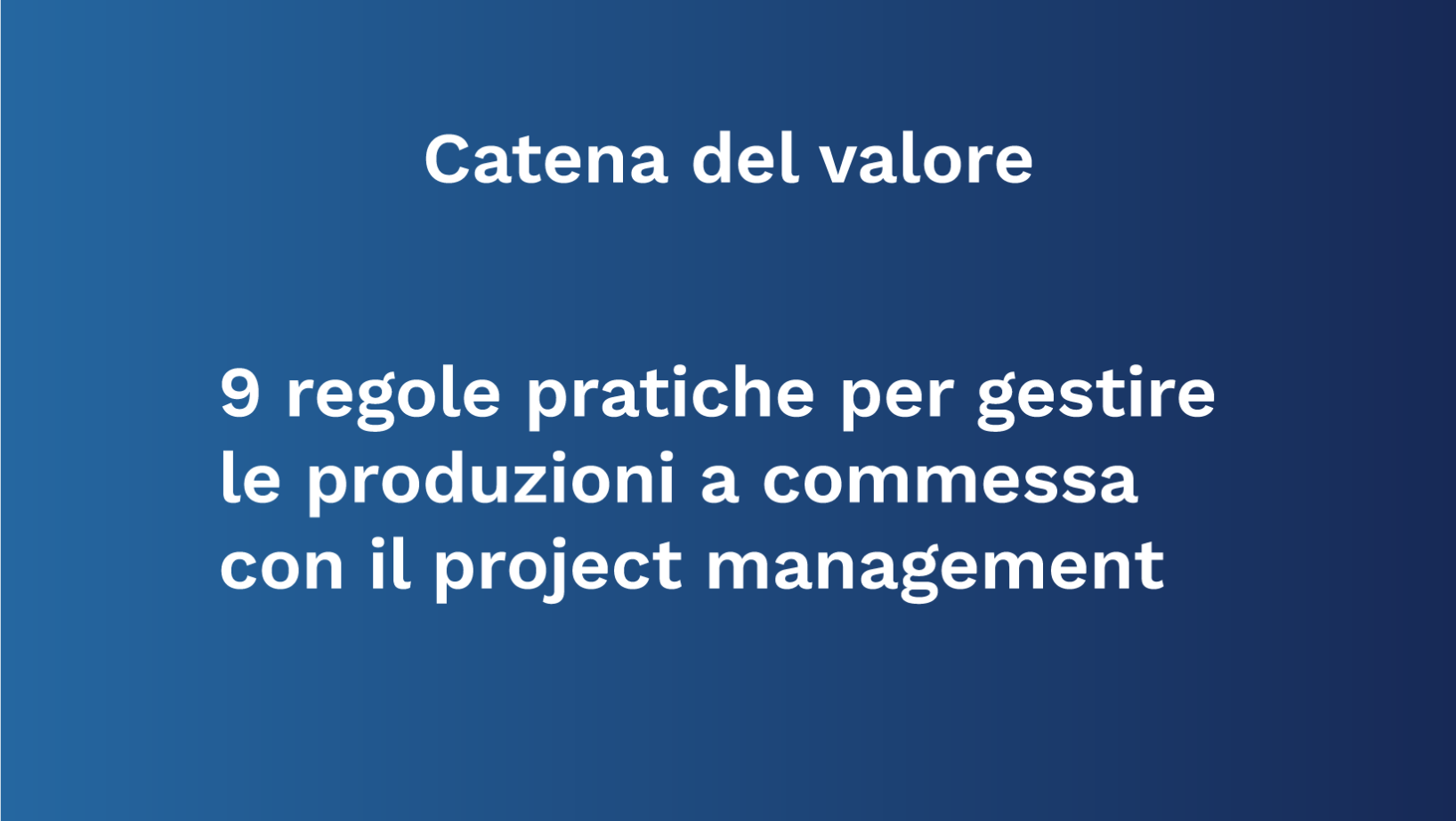
Il project management nelle produzioni custom–made
Per fronteggiare e ridurre al minimo l’impatto delle tre categorie di problemi descritte nell’articolo
“I 3 problemi della customizzazione di prodotto”, il project management è uno degli strumenti più utili.
Certo, proprio il project management, hai letto bene!
Credo che tutti noi conosciamo, almeno in maniera superficiale, in cosa consista il project management o magari, pur non conoscendolo, abbiamo provato a installare un’applicazione che ci permettesse di utilizzare i suoi metodi e tools di lavoro. Se così fosse, mi domando: come mai le aziende, al cui interno hanno uno o più project manager, soffrono dei problemi che ho presentato? Il nocciolo della questione è questo: non è tanto il project management che viene messo in discussione quanto la sua strategia di applicazione, l’execution.
Per fronteggiare e ridurre al minimo l’impatto delle tre categorie di problemi sulle produzioni custom-made descritte nell’articolo “I 3 problemi della customizzazione di prodotto”, uno degli strumenti più utili è il project management. E poco importa se parliamo di grandi impianti o di biciclette su misura, se le fasi per la realizzazione del prodotto sono tante o poche: l’applicazione di queste best practices funziona in tutti i casi. Le condivido in questo articolo, nella speranza di generare curiosità e discussione.
Le best practices del project management applicato alle produzioni custom-made
1. Evidenzia tutte le commesse che interesseranno il tuo flusso produttivo nelle prossime settimane o mesi.
Questo ti aiuterà ad avere nel tempo una stima approssimata dei carichi di lavoro di ogni area, dipartimento o fase di lavoro.
2. Fai in modo che tutti i commerciali e chi si occupa dell’acquisizione delle commesse abbiano sempre ben presente il carico di lavoro lungo tutto il flusso produttivo, da qui ai prossimi mesi.
Questo fornirà loro uno strumento utile per prevenire, per quanto possibile, già in questa fase periodi di sovrasaturazione o di insaturazione di alcune aree o dipartimenti.
3. Per ogni singola commessa, recupera i dati storici o fai una stima del carico che andrà a generare per ciascuna fase di lavoro e, quindi, per ciascuno dipartimento che attraverserà.
Questo ti permetterà di avere un’idea aggiornata del flusso produttivo e ti consentirà di prevedere con qualche settimana di anticipo se potranno generarsi dei colli di bottiglia, in quale specifico dipartimento e quando. Comunicalo costantemente ai singoli dipartimenti affinché possano organizzarsi per tempo in funzione dei carichi di lavoro attesi.
4. Crea uno strumento che ti permetta di avere, per ogni commessa acquisita, la sequenza di come i singoli componenti verranno assemblati.
Se definisci la sequenza con cui il prodotto verrà assemblato, a ritroso potrai stabilire tempi e modi di attraversamento che dovranno essere rispettati in tutte le altre fasi, dalla progettazione all’approvvigionamento fino alla costruzione di componenti.
5. Crea dei gates che permettano di rimettere in sequenza le attività da svolgere.
Non sempre e non in tutti i dipartimenti che seguono l’approccio custom-made è possibile rispettare la sequenza delle attività da svolgere, fosse anche per periodi brevi quali la giornata. I gates rappresentano uno strumento d’aiuto per rimettere in ordine le attività così come era stato stabilito inizialmente. Per esempio un gate all’ingresso di ogni dipartimento permetterà ai singoli di programmare in autonomia la propria schedulazione con una frequenza di refresh elevata e in modo che vi sia una coerenza con tutto il sistema, quindi con gli altri dipartimenti e le altre commesse.
6. Crea un sistema che regoli in modo standard il passaggio delle commesse da una fase di lavoro all’altra, da un dipartimento all’altro.
Quando le fasi di lavoro sono tante e tanti sono i componenti che le attraversano, diventa difficile gestire tutti i passaggi. Le idee possono diventare disegni, i disegni possono diventare cicli di lavoro o addirittura richieste di offerte. I componenti, a loro volta, possono attraversare diverse fasi di lavorazione, sia interne che esterne. Quando coesistono decine o addirittura centinaia di disegni, documenti e componenti che settimanalmente attraversano i dipartimenti, la mancanza di regole standard può generare il caos.
7. Crea un sistema che permetta ad ogni dipartimento di valutare, in ogni momento, la propria saturazione.
Potrebbe accadere che in un dipartimento vi sia un collo di bottiglia, senza che sia stato previsto, e che accada per una serie di concause. Implementare alcune routine di controllo permette di verificare lo stato dei fatti work in progress e di accertare l’eventuale presenza di un intoppo; questo conferisce al sistema un’elevata capacità di reazione. Quando si lavora a una commessa, la capacità di individuare tempestivamente le anomalie diventa un fattore determinante.
8. Crea un sistema centralizzato di raccolta degli allarmi generati dai vari dipartimenti.
Ogni dipartimento, in funzione della propria situazione, potrebbe rilevare delle anomalie. Talvolta potrebbero essere risolte all’interno del dipartimento senza generare allarmi; altre, invece, potrebbero non essere risolvibili in autonomia. In quest’ultimo caso è necessario prevedere un sistema centralizzato di raccolta delle anomalie, in modo che le decisioni possano essere prese nel rispetto dell’ottimizzazione globale del flusso della singola o di tutte le commesse.
9. Crea una check list standard che permetta di rispondere agli allarmi.
Un allarme può essere risolto in diversi modi. Al fine di ridurre i tempi di intervento e agire in modo coerente, quando diventa necessario prendere più di una decisione, è utile creare una check list standard che guidi nella risoluzione della problematica dalla quale è scattato l’allarme.
Una volta che sarai riuscito a trasformare ognuna di queste best practices in uno strumento di lavoro da integrare nella tua routine quotidiana. Ti renderai conto di quanto il processo di realizzazione di una commessa possa proseguire con successo quasi in autonomia, come se fosse guidato da un ‘pilota automatico’. E a te e alla tua organizzazione resterà più tempo da dedicare alla risoluzione dei problemi non standard e che richiedono soluzioni non ordinarie.
Ti sei già trovato di fronte a questo tipo di difficoltà? Come hai reagito? Raccontami la tua esperienza!